
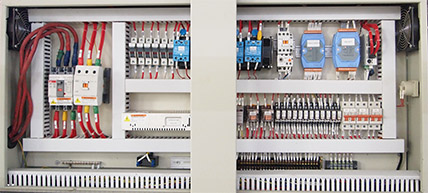
However, for mission critical or high reliability applications (i.e. Most PCBs are reflowed in an air atmosphere with great results.
#Prototype reflow oven pro#
PRO 1600 is now in a standby mode, ready for a new cycle run.ġ6 Kw (during ramp up stages of a profile)ģ1″L x 31″W x 50″H / 787mm x 787mm x 1270mm Once the reflow cycle is complete, the cover will open slowly and tray automatically exits from a heating chamber.
#Prototype reflow oven software#
PRO 1600’s control software constantly monitors actual ramp up rates and temperature inside an oven to the programmed values for accuracy. A reflow profile is then processed per the programmed settings. An operator can create custom profiles for their unique boards or simply optimize the existing profiles.Īs the Start icon is activated, the loading tray automatically slides into the reflow chamber at an adjustable and controlled speed. The software includes a library of different profiles tailored to the solder type used in the process as well as general size and mass of the circuit board. A reflow oven profile is a pre-programmed set of parameters like ramp up rate, temperature, time at set temperature, cooling method, etc., that is specific to the PCBs being soldered. Once PCBs are loaded (either single or double sided), the operator would select an appropriate reflow oven profile from the software screen. When PRO 1600 is turned on, the cover automatically opens while the loading tray slides out slowly for easy access to place down circuit boards. This is especially helpful in non-production type environments like prototype labs or for small lot runs typically saving 30 minutes or more by eliminating preheating. An operator would simply turn on the power, load the control software and the system is ready for reflow soldering with the chamber at ambient temperature. Unlike a long tunnel or conveyor type SMT reflow oven, PRO 1600 does not need to be pre-heated before it is ready to process PCBs. Various solder pastes for analysis in an R&D environment.Connector filters with fluxed preforms.Surface Mount Devices / Passive Components to ceramic substrate.Preconditioning reflows of IC’s while in extruded aluminum tubes.Wafer Bumping with Oxygen levels below 10 PPM.Copper heatsinks to PCB’s using preforms.Ceramic substrates to Gold Plated Nickel / Copper housings using preforms in an atmosphere with Various composite materials for analysis / testing.Delamination and other quality issues testing on multilayer PCB’s.Bare PCB’s to simulate profiles developed for volume production environments.
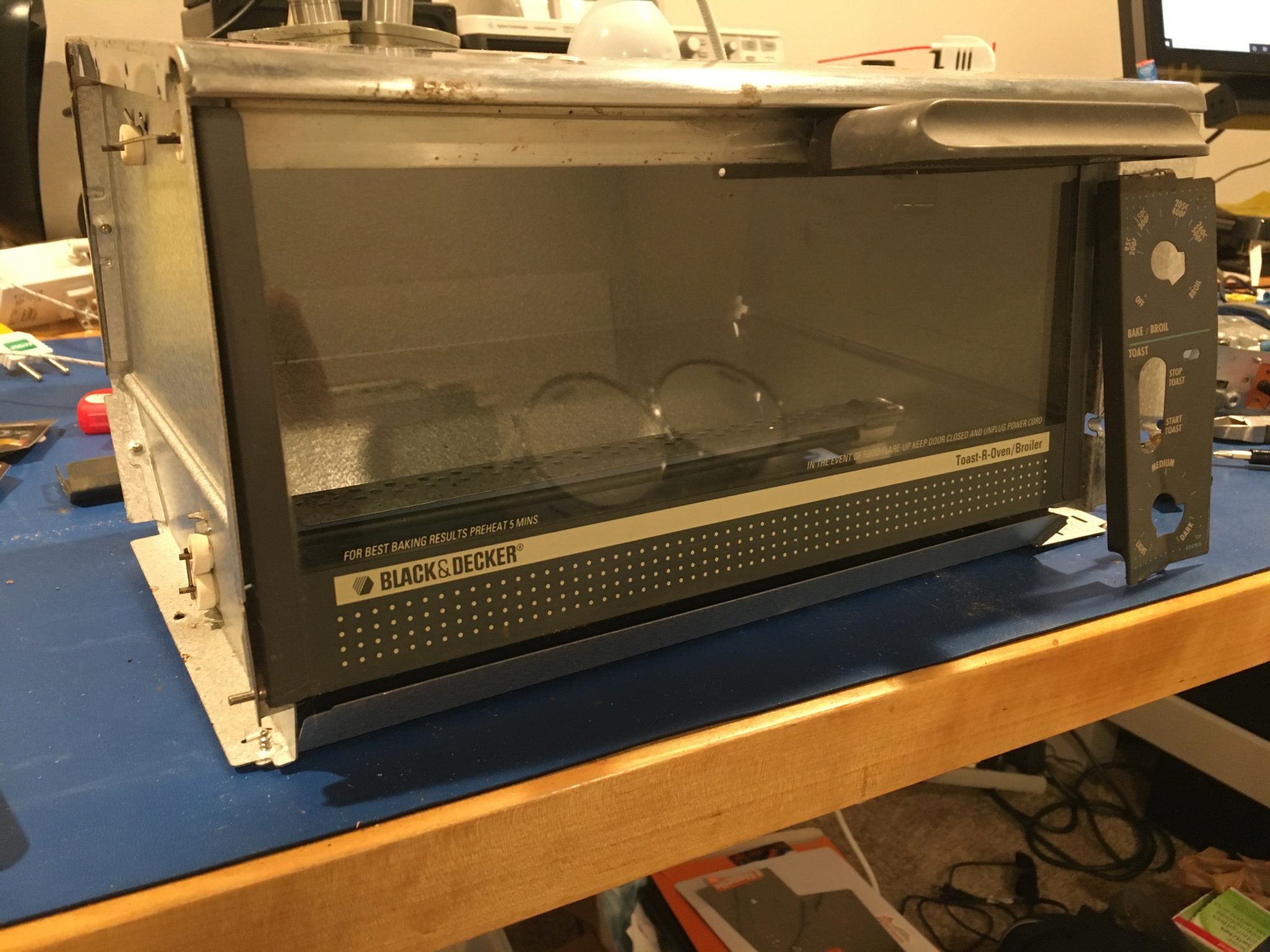
IPC-TM-650 Test Method 2.6.27 – Thermal Stress, Convection Reflow Assembly Simulation / IPC-9631.Reflow of solder preforms in an inert atmosphere.Surface Mount Devices per IPC / JEDEC J-STD-020 and JESD22-A113F standards for Leaded and Pb-Free profiles.Densely populated, metal core, and high thermal mass assemblies.Single or Double Sided PCB’s with standard or Pb-Free solders.Printed Circuit Board (PCB) assemblies requiring high quality and repeatable results in prototype – medium volumes (depending on PCB size).Increased productivity, superior performance and ease of operation make the PRO 1600 a versatile system ideal for small to medium run production, prototyping, NPI, testing or curing.Īll features of PRO 1600 SMT Typical Reflow With the optional External Thermocouple Control ( ETC), profiles may be processed based on temperature readings of the assembly, not the air temperature around it.Īn optional Video Recording and Observation Module allows taking high magnification images and recording video during a soldering cycle. Even for prototypes, this often means avoiding to spend hours of testing and debugging failed boards. Maintaining a low delta T across all of the components on the assembly ensures that they are not overheated or thermally stressed. Precise software control delivers unsurpassed temperature uniformity. Where other batch and conveyor ovens fail to meet the desired profile curve, PRO 1600 excels. It offers a unique On-The-Fly settings adjustment capability that allows creating and optimizing profiles all in a single pass. Sealed heating chamber enables ramp up rates of up to 4° Celsius/second from ambient and programming of up to 10 profile zones. PRO 1600 is very user friendly in terms of profile creation and modification. It has been designed for reflow soldering of even the most challenging applications including metal core, high thermal mass, RF/microwave housings, wafer boards, and ceramic assemblies. PRO 1600 is a forced air / nitrogen convection reflow oven with a small footprint measuring only 31″ x 31″ (80cm x 80cm).
